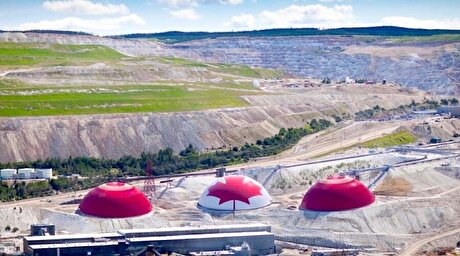
Turkish steelmaker Atakaş released the final acceptance for six bell annealing furnaces in operation at Iskenderun.
The supply consisted of the addition of six new bases (three furnace bells and three cooling bells) to the existing BAF eight-base line installed and started-up by Danieli in 2018, along with the complete cold-strip complex.
The upgraded facility now is capable of processing prime-quality annealed sheet products of cold-rolled carbon steel for the general and automotive markets – CQ, DQ, DDQ and EDDQ quality, according to the related international standards.
Maximum diameter of coils is 2,000 mm, with strip thickness ranging from 0.3 up to 2.0 mm.
Up to five coils (100 tons) are charged on the treatment base, which is enclosed by a stainless steel inner cover that maintains a perfectly sealed working atmosphere.
The working atmosphere is purged with nitrogen, then filled with hydrogen, which is used to speed up heating and cooling times, to protect coil surface from oxidizing and to ensure brightness.
A heating bell is positioned on the base to start the heating and soaking phase of the cycle, reaching the metallurgical transformation temperature (up to 750 °C) with +/- 10°C uniformity.
The heating bell is removed with the crane and a dedicated cooling bell is then placed over the inner cover to reduce the cooling time to the minimum, maximizing the production rate.
At the end of cycle (typically 35/40 hours in total) the treated coil features perfect mechanical/metallurgical properties, homogeneous between surface and coil center.
All process parameters, as well as safety functions, are managed by Danieli Automation control system.
Contractual performances including consumption and emissions were achieved.
Erection and commissioning phases have been optimized so that the plant stoppage for the integration of the new bases was reduced to two weeks.